With years of renewable energy experience and access to 200 GW of wind and solar data, Clir has the ability to compare asset performance across our client portfolio. In our investigations, we’ve discovered persistent anomalies that impact turbine performance, along with other opportunities for optimization. Many are simple fixes or updates that can be managed through the wind turbine control system.
At any given wind turbine, the alignment between the nacelle and the wind direction varies naturally over time. The nacelle will rotate or yaw when the difference between the nacelle and the wind direction exceeds preset parameters. If a wind turbine spends too much time misaligned, wind power production will be diminished. This simple, yet persistent, problem is one we frequently encounter.
Turbine yaw control
The turbine yaw system refers to the overall system that controls the direction a wind turbine’s nacelle is pointing in relation to the direction of the wind. This is typically measured through the nacelle anemometer, and the difference between the wind direction and the nacelle position is often referred to as the yaw error. When the yaw error is at zero degrees, it is aligned perfectly with the wind for power production.
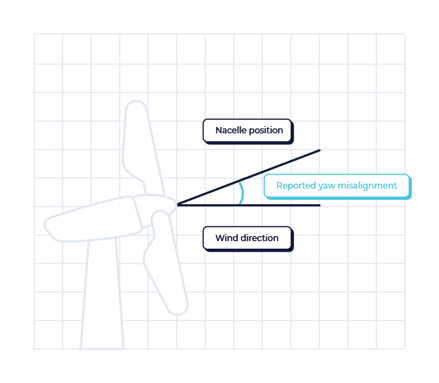
Since the wind direction changes frequently, it’s important for the yaw error to be minimized. Some dynamic yaw misalignment is standard, but too much can result in production loss. Optimized yaw control can reduce the frequency of large yaw misalignments. However, tracking wind changes too closely can cause wear on components due to frequent direction changes.
Clir’s dynamic yaw analysis
The Clir platform uses a dynamic yaw benchmarking and analysis tool to identify and analyze yaw control error distributions. Using 10-minute SCADA data, it analyzes the turine yaw distribution and identifies if there is an excessively wide distribution at any turbine on site.
Typically, dynamic yaw misalignment is distributed and centred on zero degrees. A wider distribution indicates that the turbine spends more time misaligned with the wind. In contrast, a narrower distribution indicates that the turbine is tracking the wind more closely.
Reviewing yaw misalignment
In an analysis of the dynamic yaw control at a 60 turbine wind farm in the United States, Clir discovered that two turbines were following the wind more closely than other turbines. The yaw control of those turbines was in line with industry-standard, tracking the wind within an eight-degree error band.
While the other turbines at the farm were tracking the wind consistently, the yaw error bands of operation were wider. Instead, it occurred at eight degrees from the nacelle measured wind direction — 16-degree total width. Clir determined that if all wind turbines were controlled to industry standard, the estimated increase in production would be 4,500 MWh per year.
Yaw correction
In the above scenario, correcting the turbine yaw misalignment was a simple fix. With the data available from Clir’s analysis, the operator was able to find and fix the parameter setting that differentiated the yaw controls across the turbines.
With benchmarking data and data-driven performance improvements, owners can discover persistent, industry-standard performance errors that may be impacting their portfolio. Recognizing and fixing these issues can increase AEP and decrease asset depreciation. Improving annual energy production, in conjunction with optimized operational management, can result in better financing options.